MS3 develops the technology for future manufacturing processes and new products by a science based engineering approach focused on material- and system behaviour and robust optimization.
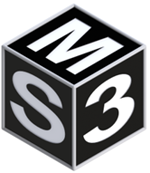
A well-known quote of Theodore von Kárman states “Where scientists study the world as it is, engineers create the world that never was.” Creating new and better materials and products as well as the machinery required to make these products is the focus of the MS3 department. Manufacturing new products and/or developing new processes requires a profound scientific understanding of the materials and their interactions throughout the complete life cycle: during production, use and after service life.
The mechanics of materials and systems for small and large deformations, in quasi-static and dynamic conditions provide the background for our operations. The products and the manufacturing systems are typically from the microscopic to the macroscopic scale, where the underlying research also deals with submicron features.
Industry provides a further context for the department. Our students are trained to solve industry’s problems of today and tomorrow and our research is directed to develop the technology needed to be successful in the long run. Complex multi-physics problems are analysed and solutions are developed by the synthesis of scientific building blocks. Three themes are distinguished in our research, related to materials, systems and optimisation methods.
The mission of MS3 is “Manufacturing the Future”. MS3 develops the technology for future manufacturing processes and new products by a science based engineering approach focused on material- and system behaviour and robust optimization.
Research
Research within the department of Mechanics of Solids, Surfaces & Systems (MS3) addresses the scientific and engineering aspects of the strongly related “triangle” of (i) material (behaviour), (ii) production and (iii) products, where ultimately the performance of all aspects is of crucial importance. Based on this we defined three research themes within MS3:
Material behaviour is one of the cornerstones of the MS3 research. Characterisation, modelling and creating the paths to engineering solutions are a key expertise for a wide range of materials and interfaces. Technical materials from elastomers, polymers, metals, ceramics to composite materials as well as biological tissues are subject of research. Fibrous materials are of special interest. Typically we use and develop models and experiments iteratively to complete our understanding of the physics involved, in order to design better processes, materials and, in the end, a better product.
Both bulk and surface properties are investigated to improve processing and performance, but also functionalization methods are developed to create so-called smart materials (often a system in itself exhibiting multiple physical phenomena at the same time). The chairs involved in MS3 cover a wide range of expertise on material behaviour, from linear elastic to highly nonlinear and extremely anisotropic properties, from static to dynamic and long term fatigue performance, from linear thermal properties to highly rate and state dependent phenomena, for instance as encountered during pulsed laser processing.
System behaviour is crucial for both the products and production researched within MS3. Characterisation, identification and multiphysics (dynamic) modelling are the expertise required to ultimately achieve designs that meet their specifications. The models needed in this context cover a large range of complexity. On the one hand, detailed knowledge as e.g. from MS3 theme on materials must be available to accurately describe the static and dynamic behaviour of a component in a system. On the other hand, for system level design there is a need for models with less detail that nevertheless capture the influence of design parameters on system performance.
This wide range of detail can be identified in the various modelling techniques researched within MS3. In general static or dynamic properties of components, processes or systems are considered. Specifically considered processes are the thermo-mechanical analysis of forming processes and laser materials (surface) processing. Relevant for component behaviour are the dynamic behaviour of fabrics and the mechanical and thermal modelling of surfaces and interface layers for friction and wear between statically or dynamically interacting components. Dynamic (system) properties involve vibro-acoustic analysis, flexible multibody system dynamics including multiphysics coupling, mechatronic systems (i.e. mechanical systems with sensors, actuators, power generation and (digital) control), as well as dynamics based structural health monitoring and condition monitoring. Characterisation and (system) identification are used to evaluate realized systems. Model-based design approaches are being developed and applied e.g. for complete structural health systems and high performance manipulation equipment.
The themes Material Behaviour and System Behaviour include modelling of materials and systems. If quantitative models are available to predict the behaviour of materials and systems, products and processes can be designed with a specified performance. This is often an iterative process in which the design is changed until the requirements are satisfied. With a focus on product and process performance within MS3, optimization is a natural extension of the modelling activities within the group. Since optimized structures are often more critical, where materials are used to the limit, it is essential to include reliability and robustness with respect to material and process scatter in the optimization objective.
Hence, in robust optimization uncontrolled variation of relevant parameters is included in the optimization of products and processes. Ideally, full statistical distributions of parameters, including correlations, are used. In other cases, such as e.g. specified manufacturing tolerances, minimum and maximum values are used. Robust optimization requires a large amount of direct simulations and therefore often meta-models or reduced order models are required to limit calculation times.
The goal is to obtain safely operated and economically viable products and processes, where ‘products’ can also relate to engineered materials and surfaces.
News and events
Organisation
The department is chaired by Prof.dr.ir. E. van der Heide and the first focal point for internal affairs within the university. Dr.ir. G.R.B.E. Römer is portfolio manager research and the primary contact person for industrial contacts. The primary contact person for educational matters is the portfolio manager education Dr.ir. R. Loendersloot.