Overview
The chair of manufacturing systems deals with the planning and operation of manufacturing systems respectively factories in diverse industry sectors. This includes the interaction of different processes over the process chain but also with other factory elements like technical building services and also the building itself. Thereby all material, energy and information flows need to be considered in an integrated manner. Besides technological developments, digital methods and tools play a crucial role in factories of the future. Even more, obviously the technical and economic performance but also environmental and social perspectives need to be taken into account.
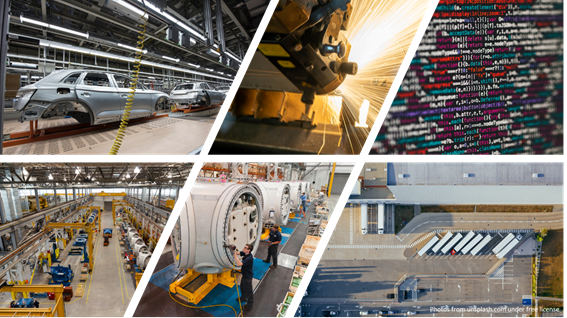
Smart manufacturing solutions based on Cyber Physical Production System (CPPS) framework Cyber physical production systems (CPPS) are one core element within the digital (r)evolution of manufacturing systems and bear significant potential for improvement. CPPS stand for the connection of the physical manufacturing world with an up-to-date virtual (cyber) representation which can be used for advanced decision support and control. Given that, the chair of manufacturing systems works on innovative CPPS based solutions that include data acquisition strategies (e.g. integration of innovative sensors), their combination with feasible digital models (e.g. based on machine learning or factory simulation) and their transfer towards improvement of future factories (e.g. through expert systems, VR/AR, control implementation).
Methods for factory planning and operation The planning and operation of factories comprise of diverse, interacting fields of action that are covered by the chair of manufacturing systems in research but also teaching. Examples are facility/layout planning, production planning and control (PPC), quality management, lean management or maintenance questions.
Innovative manufacturing systems/factory concepts New production related challenges (e.g. lot size 1, necessary resilience of value chains, energy transition) and ongoing technological advancement (e.g. additive manufacturing, advanced robotics) call for innovative concepts for future factories. Examples are manufacturing systems that need to address the trade off between efficiency and an increasing demand on flexibility regarding product variants and volatile volumes.
Sustainable manufacturing Without the question, just looking at the technical and economic performance of manufacturing system is not sufficient nowadays. Having in mind the concept of sustainability, all three dimensions – economy, environment, society – need to be taken into account simultaneously. In context of environmental sustainability this includes e.g. the development of technological and methodological solutions to improve of energy and resource efficiency through all factory elements.
Human factors in manufacturing systems Despite digitalization and automatization being strong change drivers in manufacturing, the human will still play a central role in future factories. Technological developments, demographical change, strong competition and rising concerns regarding health issues more than ever call for innovative solutions here as well. Fields of actions are e.g. occupational health and safety, ergonomics/workplace design and also (continuous) learning concepts.