View as:ListGridSummary
Scientific Staff
prof.dr.ir. J.M. van Oort (Hans)prof.dr.ir. S. Vanapalli (Srini)
dr. M.M.J. Dhalle (Marc)
dr.ir. M. A. J. van Limbeek (Michiel)
A. Nijhuis (Arend)
prof.dr. T. du Pree
dr. C. Falsetti
dr.ir. A.U. Kario (Anna)
PhD Students
H. Beens (Harro)G. Anniballi (Giulio)
S. Khute (Sahadasan)
R.M. Metsch (Roel)
J. van Steenlandt (Jan)
W.M. Verbruggen (Wouter)
M.C.K. ter Schure (Margreet)
Adam Kovacs
Ruber Keijzer
ir. K.W. Lotze (Koen)
A. Xhahi (Arvi)
R.M.A. Spijkers (Rick)
N. Toolboom
I. Hanze
Technical Staff
ing. W.A.J. Wessel (Sander)C.H. Vermeer (Cris)
ing. H.J.G. Krooshoop (Erik)
ing. H.J. Holland (Harry)
Scientific Staff

prof.dr.ir. J.M. van Oort (Hans) Full Professor

prof.dr.ir. S. Vanapalli (Srini) Applied Thermal Sciences (ATS) Group Leader

dr. M.M.J. Dhalle (Marc) Associate Professor

dr.ir. M. A. J. van Limbeek (Michiel) Assistant Professor

A. Nijhuis (Arend) Researcher

prof.dr. T. du Pree Nikhef

dr. C. Falsetti Assistant Professor (Guest) - TU Delft

dr.ir. A.U. Kario (Anna) Assistant Professor (Guest)
Emeritus

prof.dr.ir. H.J.M. ter Brake (Marcel) Full Professor

prof.dr.ir. H.H.J. ten Kate (Herman) Professor Emeritus at UT and Honorable Member, Contributing Retiree at CERN-Geneva
Secretariat
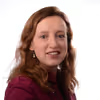
K.J.H. Munnink (Karen) Management Assistant EMS-TNW
PhD Students

H. Beens (Harro) PhD Candidate

G. Anniballi (Giulio) PhD Candidate

S. Khute (Sahadasan) PhD Candidate

R.M. Metsch (Roel) PhD Candidate

J. van Steenlandt (Jan) PhD Candidate

W.M. Verbruggen (Wouter) PhD Candidate

M.C.K. ter Schure (Margreet) PhD Candidate
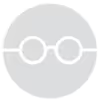
Adam Kovacs Industrial PhD Candidate
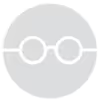
Ruber Keijzer PhD Candidate
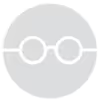
ir. K.W. Lotze (Koen) PhD Candidate

A. Xhahi (Arvi) Junior Researcher

R.M.A. Spijkers (Rick) Researcher
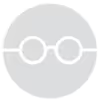
N. Toolboom PhD Candidate
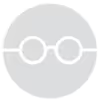
I. Hanze PhD Candidate
Researcher

G.S. Santos Tomás PhD (Gonçalo) Post doctoral researcher

Jurgen Rietberg Junior Researcher
Technical Staff

ing. W.A.J. Wessel (Sander) Research Engineer, Lab Supervisor

C.H. Vermeer (Cris) Research Engineer, Lab Supervisor
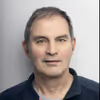
ing. H.J.G. Krooshoop (Erik) Research Engineer, Lab Supervisor

ing. H.J. Holland (Harry) Research Engineer
Superact

Ing. Ruben Lubkemann Research Engineer

dr.ir. S.J. Otten (Simon) Researcher (Guest)

J. Leferink (Jorick) Research Engineer
MSC Students

Laura Rouwenhorst Master
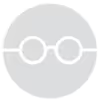
Jurrie Bruggeman Master
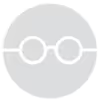
Wouter Eppink Master
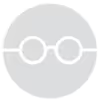
Gerjan Wennemars Master Thesis
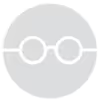
Aide Flores Fernandez Master
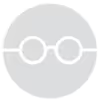
Rik van Ingen Master
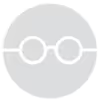
Thomas Hanhart Master
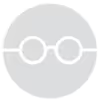
Annelies Klaassen Master
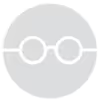
Nathan van Dusschoten Master
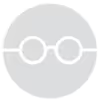
Nienke Buskens Master
BSc Students
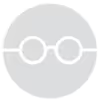
Imre Kersting BSc thesis
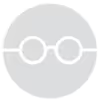
Filip Zijda BSc thesis
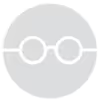
Koen van der Horst BSc thesis
Scientific Staff
prof.dr.ir. J.M. van Oort (Hans) Full Professor
Personal page prof.dr.ir. S. Vanapalli (Srini) Applied Thermal Sciences (ATS) Group Leader
Personal page dr.ir. M. A. J. van Limbeek (Michiel) Assistant Professor
Personal page Emeritus
prof.dr.ir. H.H.J. ten Kate (Herman) Professor Emeritus at UT and Honorable Member, Contributing Retiree at CERN-Geneva
Personal page Secretariat
K.J.H. Munnink (Karen) Management Assistant EMS-TNW
Personal page PhD Students
M.C.K. ter Schure (Margreet) PhD Candidate
Adam Kovacs Industrial PhD Candidate
Ruber Keijzer PhD Candidate
N. Toolboom PhD Candidate
I. Hanze PhD Candidate
Researcher
G.S. Santos Tomás PhD (Gonçalo) Post doctoral researcher
Personal page Jurgen Rietberg Junior Researcher
Technical Staff
ing. W.A.J. Wessel (Sander) Research Engineer, Lab Supervisor
Personal page C.H. Vermeer (Cris) Research Engineer, Lab Supervisor
Personal page ing. H.J.G. Krooshoop (Erik) Research Engineer, Lab Supervisor
Personal page Superact
dr.ir. S.J. Otten (Simon) Researcher (Guest)
Personal page MSC Students
Laura Rouwenhorst Master
Jurrie Bruggeman Master
Wouter Eppink Master
Gerjan Wennemars Master Thesis
Aide Flores Fernandez Master
Rik van Ingen Master
Thomas Hanhart Master
Annelies Klaassen Master
Nathan van Dusschoten Master
Nienke Buskens Master
BSc Students
Imre Kersting BSc thesis
Filip Zijda BSc thesis
Koen van der Horst BSc thesis