
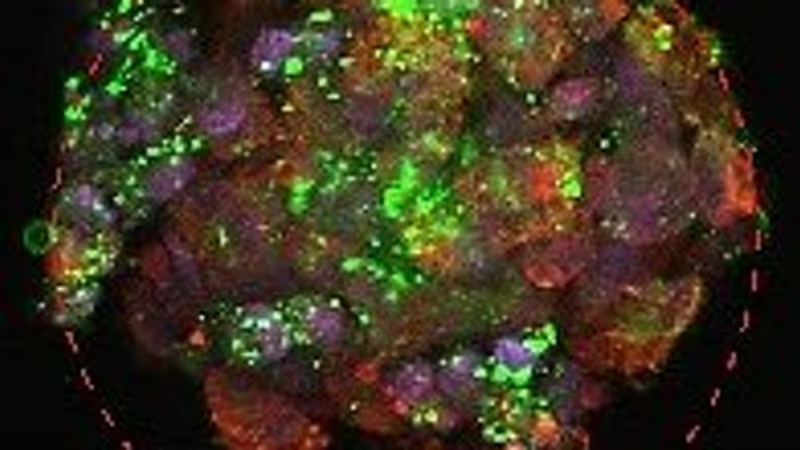
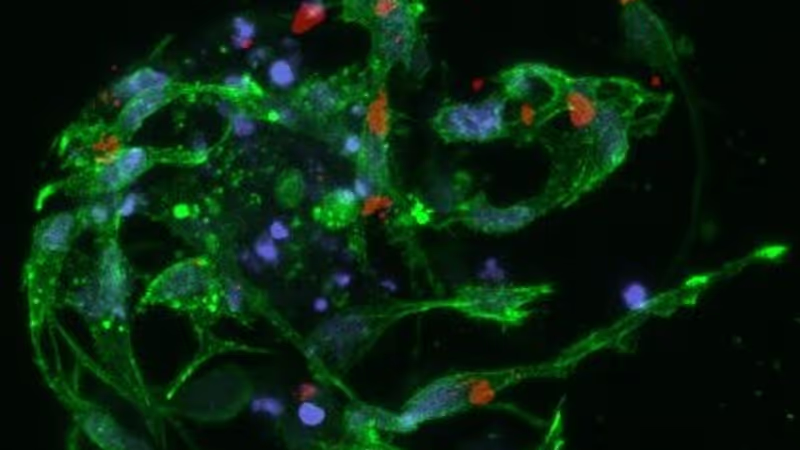
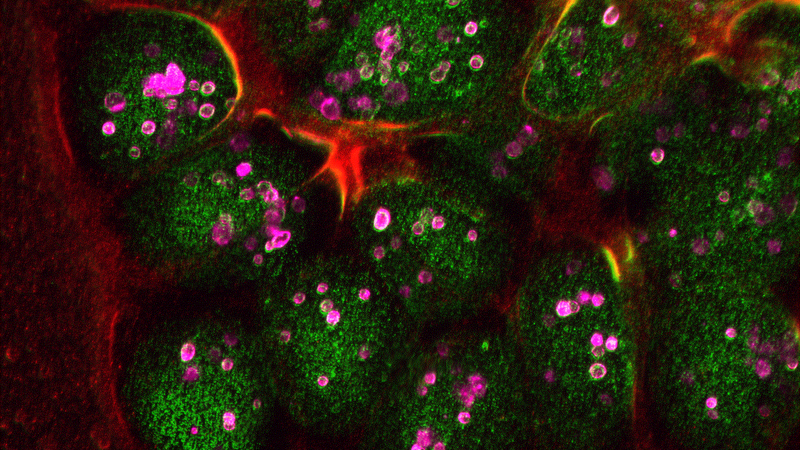
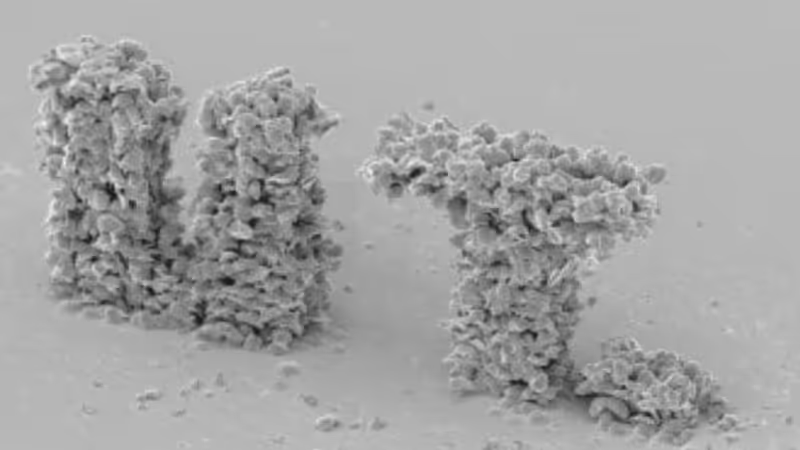
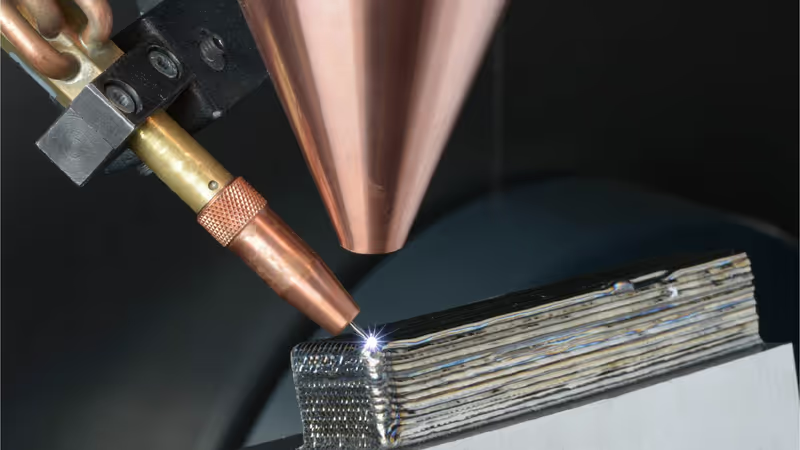
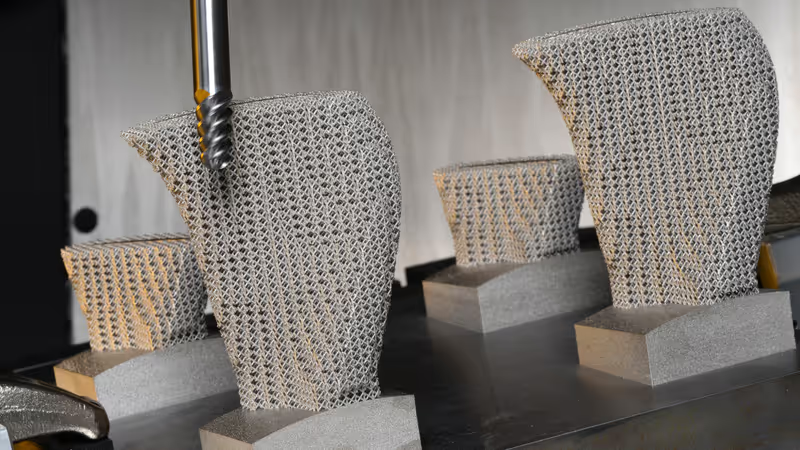
When: 23rd of May 2019 from 9:30 to 17:30
Where: Horstring, C 101
Additive manufacturing (AM) is the general term for printing processes, e.g., 3D printing, rapid prototyping or layer manufacturing. Such processes involve several technologies used to make 3D objects with the overlaying of single or multi-material compositions. AM includes the use of 3D computer-based models for the design of specific functional equivalencies mimicked by the AM equipment until fabrication of the 3D object. Polymers, metals, ceramics or multi-compositions are endless. For example, AM is used in medical applications (bioprinting, implants), industrial (aerospace, automotive, construction), paleontology, forensics, and rapidly expanding to different fields like food, energy and catalysis industries which constantly demand disruptive applications. Across length scales, AM technologies are becoming very accurate, and they can be used for the fabrication of mesoscale prototypes (nano/micron-sized features) up to large scale products (meters-sized).
Workshop aim
During the workshop, several principal investigators from different faculties will present their projects. The goal is to provide an overview of all the activities in AM to strengthen the community of people working in the field of nano/micro/macro AM. This workshop will help to connect AM researchers, resulting in new ideas, cross disciplinary cooperation and projects.
Registration
Participation is free of charge. Registration is mandatory.
Click here to register for the workshop.
Program
Click here to see program details.
Invited speakers
- Arjen de Hollander
Integrated Manufacturing solutions for Industrial Additive Production
The Fraunhofer Project Center at the University of Twente is a joint venture of three partners: the University of Twente, the hosting university, the Fraunhofer-Gesellschaft represented by its Fraunhofer Institute for Production Technology IPT in Aachen, Germany and Saxion University of Applied Sciences. The central task of the Fraunhofer Project Center is to transfer current research in advanced manufacturing directly into industrial practice. For this, we focus on the development of technological solutions in the area of production processes, production equipment, digital manufacturing and manufacturing value chain organization. Together with industry, we build synergies to achieve high-tech excellence within the fourth industrial revolution and to train the high-tech talents of tomorrow.
One of the focus points is Industrial Additive Production. An insight in the project approach and the current developments in our Pilot Project 3D2SKY will be presented.
- Claas Willem Visser
In-Air Microfluidics Enables Rapid Fabrication of Emulsions, Suspensions, and Multi-Scale Materials
Microfluidic chips enable reproducible generation of complex droplets and particles, but have a low throughput that blocks their industrial use. Furthermore, the resulting particles cannot be readily used as building blocks for solid (meta)materials, as they are contained by a liquid phase. Here we address these limitations by ejecting a train of droplets into the air and manipulating their properties by impact of a second liquid jet. The surface tension of the jet was reduced, so that it encapsulates the droplet by Marangoni spreading. Subsequent on-the-fly manipulations, including solidification and controlled deformation, enable fabrication of monodisperse emulsions, particles, and fibers with diameters of 20 to 300 μm at rates that are 10 to 100 times higher than chip-based droplet microfluidics. Deposition of the partly-solidified droplets onto a solid substrate enables one-step manufacture of three-dimensional (3D) multiscale materials. For example, we demonstrate an artificial pancreatic tissue in which each solidified droplet forms a controlled micro-environment in which MIN6-cells maintain their viability and capacity to produce insulin. In-air microfluidics, as we name this approach, enables fabrication of controlled particles and capsules at industrially relevant rates of up to 6 ml/minute/nozzle. I will present recent results including the fabrication of composite (magnetically and chemically active) hydrogel Janus particles for enzymatic cascade reactions, and sketch how In-air microfluidics may contribute to one-step fabrication of multi-scale materials with controlled mechanical, biological, optical, or thermal properties.
- Gijs Krijnen
Additive Manufacturing of Physical Sensors
Where modern high-tech sensors are primarily fabricated from stiff materials using subtractive technologies, nature seems to build soft and distributed sensing structures by additive methods. Current MEMS, NEMS and precision engineering approaches increasingly provide the resolution but not necessarily the materials flexibility nor the freeform 3D shapes found in nature.
In our research we investigate multi-material 3D printing in order to make flexible, physical, embedded sensors with applications in (soft) robotics, prosthetics and orthoses. Examples are bio-potential electrodes and arrays, e.g. for sEMG, force-myography sensors, tactile, force, flow and rotation-acceleration sensors. Sensing is primarily based on resistive and capacitive read-out. We fabricate these sensors by co-printing conductive (carbon black doped) and non conductive thermoplastic poly-urethane (TPU). Materials and equipment are relatively affordable and well positioned for use in educational settings. Nevertheless the structures obtained ask for a range of characterisation techniques and form a rich ground for (academic) research.
In the presentation we will elaborate on the proposition to fabricate sensors by Additive Manufacturing and give various examples of sensors that we have investigated in the last two years. Additionally we will briefly introduce the physical richness obtained when traxels (track elements) of conductive material are loosely interconnected at their interfaces by looking at the resulting impedances of multi-traxel structures.
- Han Gardeniers
Additive Manufacturing of mesoscale structures with chemical applications
The ability to accurately position nanoscale active elements in flow-through mesoscale structures with high symmetrical order is instrumental in streamlining vital molecular or energetic paths in chemical applications. 3D periodicity minimizes spatial variations in mass transport, whereas mesoscale control of the location of active sites opens a way to tune activity and chemical functionality. Additive Manufacturing is probably the only method that offers the desired freedom in shape, symmetry and composition.
The MCS group is exploring two types of AM for the purposes mentioned above: electrospinning and two-photon stereolithography. This contribution will give an overview of the principles and manufacturing results of these two techniques. For the electrospinning of nanowire arrangements, two innovative approaches will be highlighted: the use of microfluidics and micromachined nozzles to define the composition and dimensions of the nanowires, and the implementation of auxiliary electrodes at the collector side, to enhance nanowire positioning accuracy.
- Henk Gooijer
Additive Manufacturing on Textiles
The research area of the research group Smart Functional Materials is textiles. The research group has 3 research lines:
- Sustainability
- Smart Textiles
- Surface modification
In the research lines surface modification and smart textiles, research is executed in the area of additive manufacturing. Within the research group three additive manufacturing techniques are available: Piezo drop-on-demand printing, valve jet printing and ‘classical “3D-printing. The research is always executed in close cooperation with companies, as e.g. SPGprints, Ten Cate, Tanatex, Schmits, Teijin and Artex.
Piezo, drop-on-demand, printing
The research group has a Fujifim Dimatix lab printer, which is used for the development and testing of inks and the development of applications. The substrate printed on is always textile or textile related and the printing is focussing on the functionalization of surfaces: UV-curing coatings, conductive tracks, self-cleaning and soil-repellency.
Valvejet technology
Recently, the research group has acquired a Zimmer Chromojet lab printer, which is a mechanically driven inkjet printer enabling the application of larger amounts of chemicals than DOD-printing. The first research with this technology is focussing on applications as conductive circuits, 3D-structurizing, application of microcapsules and water repellency.
3D-printing
In the area of 3D-printing, the research is not focussing on 3D-printing of textile like materials, but on the printing of 3D-structures on textiles, examples are printing of connectors, device housings and coating of conductive tracks.
During the presentation, examples and applications of the 3 different application techniques will be shown and discussed.
- Ian Gibson
Taking AM Seriously: The Move from Prototyping to Manufacturing
For many years, additive manufacturing (AM) technology has been seen by most as laboratory equipment that is mainly used to assist the product development process by creating prototypes. Nowadays, it is well known that the material properties and machine capabilities are such that many more applications are possible, including specifically the ability for direct production. However, it is really only recently that some of the technology vendors have seriously looked at their machines with regards to how they can be used as part of an integrated shop floor environment. This presentation will discuss these developments and how this influences our future research agenda in this area.
- Ivo Vrooijnk
Applied Research on (Concrete, Metal, Plastic) AM Applications
At Saxion University of Applied Sciences the research group Industrial Design is involved in various projects on Additive Manufacturing (AM). Driven by questions and interest of SME’s, design offices, large industrial companies and institutes like hospitals, we mainly focus on applications and related design questions. This resulted in some interesting cases and research results on metal, concrete and of course plastic AM which we are happy to share.
For instance, while we researched many different topics related to concrete 3d printing like recipe, mixing in line, undercuts, reinforcement, the most interesting turned out to be the search for relevant (interesting?) applications within design constrains. On metal AM we’ll share some samples of the discovery tour companies experienced bringing in cases they thought to be of interest applying metal 3D printing. And: how can this case-oriented approach produce general applicable results? And finally, the samples we show on plastic printing concerns our cooperation with hospital MST.
- Jai Prakash
Advanced 3D Bioprinted Tumor Models
Tumors are not made of only tumor cells but contain stromal cells in their surrounding which help tumor cells to growth, migrate and become resistance to drugs. Therapies often fails in clinics despite successful results in vitro and in vivo. We have now developed novel 3D bioprinted tumor models in which we can bioprint different cells from the tumor microenvironment with different geometries in high precision to mimic the actual tumor microenvironment. As an example, we have recently bioprinted a glioblastoma model by combining macrophages and tumor cells. Here, we showed that novel 3D-bioprinted mini-brains consisting of glioblastoma cells and macrophages could be used as tool to study the interactions between these two cell types and to test therapeutics that target this interaction. Tumor cells showed the gene profile similar to the clinical samples from glioblastoma patients. Then, we showed that our 3D bioprinted tumors were resistant to the chemotherapy. Finally, we demonstrated how therapeutics can inhibit the interaction between GAMs and tumor cells resulting in reduced tumor growth and more sensitivity to chemotherapy. In conclusion, 3D-bioprinting provides great opportunities to create novel tumor models to improve our understanding of tumor biology and for evaluating novel cancer therapeutics.
- Jeroen Leijten
Creating Advanced Bio-Inks Using Microfluidics to Engineer Multiscale Tissues
The modular design of tissues is of indispensable importance for proper organ function. For example, extracellular matrix is naturally produced in a modular way. Cells are entrapped in a thin layer of pericellular matrix, which in turn is located in a bulk of extracellular matrix. These two matrices are highly distinct in their biochemical and biophysical properties; while the pericellular matrix interacts with the cells, the extracellular matrix gives rise to organ level characteristics. Incorporating such a modular design into biomaterials is expected to allow engineered tissues to more accurately emulate the behavior of native tissues. However, recreating pericellular matrix has remained a grand challenge as it requires the coating of individual single cells in a micrometer thin layer of biomaterial. To overcome this challenge, I have developed microfluidic droplet generation platforms for the production of enzymatically crosslinked single cell microgels that were mere micrometers larger than the single cell they encapsulated. Using this platform, I engineered 3D single stem cell microniches with on-demand tunable biophysical and biochemical properties to controllably program stem cell differentiation along chosen lineages. For example, the microgels’ Young’s modulus can be accurately tuned from 2 to 50 kPa. Single cell analysis revealed that softer microgels stimulated adipogenesis, while stiffer microgels induced osteogenesis. Temporally stiffening the microgels revealed that the first three days of differentiation where of key importance for stiffness-induced stem cell fate decisions. We then combined our microgels with distinct biomaterials to create advanced bioinks. This modular approach effectively uncoupled the engineered tissues pericellular and extracellular environments. This allowed for an unprecedented control over the design and behavior of the living implant. Lastly, to endow our tissues with macroscale properties such as tissue shape, we used our bioinks in combination with various biofabrication techniques such as injection molding, photolithography, and 3D printing to engineered multiscale hierarchical living implants. In short, I here present several microfluidic microgel-based concepts that are focused on advancing the engineering of multiscale hierarchical tissues constructs.
- Jeroen Rouwkema
Additive Manufacturing of Self-Organizing Vascular Networks
Engineered tissues offer a great promise as an alternative for donor tissues, for which the supply is not meeting the demands. However, currently, the clinical application of engineered tissues is hampered. The integration of engineered tissues after implantation is limited due to the lack of a vascular network, resulting in nutrient limitations and possibly cell death. A possible strategy to solve this problem is to include a vascular network in the engineered tissue before implantation. Optimally, such a vascular network should be organized over different scales, including larger structures to transport blood into the tissue and small capillaries to distribute the blood to all the cells.
In order to achieve multiscale organized vascular networks within engineered tissues, we are developing a 3D embedded bio-printing approach to spatially control the presence of vascular cells within tissue analogues, as well as the environment in which the cells reside. This can be seen as a starting situation which will remodel and mature over time. To further guide the organization of the vascular network over multiple scales, both chemical and mechanical cues are included. With this approach, our aim is to control tissue remodeling and maturation, resulting in a vascular network that resembles a vascular tree.
- Matthias Feinaeugle (& Gert-Willem Römer)
Laser-based additive manufacturing at the Chair of Laser Processing - from sub-microns to metres
Additive, laser-assisted manufacturing techniques studied at the Chair of Laser Processing at the University of Twente can produce parts stretching from micrometres to metres and covering a broad range of materials with a special focus on the deposition of metals.
In the first part of the presentation, we show advances in laser-induced forward transfer (LIFT), a type of ‘functional’ 3D printing, that uses ultrashort pulsed lasers to fabricate parts with micron-size features. The LIFT technique can be used for structures from metals, semiconductors, dielectrics, ceramics, polymers and even biomaterials, is contactless and can be carried out at ambient atmosphere. At Twente, our aim is to produce very small, pure and free form metallic micro structures required for applications in microfabrication, such as in MEMS or electronic chips.
Furthermore, we will present results of laser metal deposition (LMD) or laser cladding, a powder blown laser fabrication process, used to additively manufacture components layer by layer, with a single layer thickness ranging from 0.2-2.0 mm. Fabrication throughput of LMD is several kg/hour intended for larger, metre-scale parts. LMD is employed for a broad range of compositions, e.g. Ti-, Ni- and Fe-based metal alloys with intended applications in biomedical, aerospace and metal forming sectors. In addition, extreme fast cooling of the laser melt yields a highly refined microstructure, improving thermo-mechanical properties for high temperature applications. A recent addition of a 10 kW Trumpf laser with special beam shaping possibilities will allow an increase in fabrication throughput and to implement extreme high-speed laser additive manufacturing (EHLA).
- Nils Knofius (& Matthieu van der Heijden)
Additive Manufacturing in After-Sales Service Supply Chains
After-sales service supply chains support the maintenance of advanced capital goods during their life cycle of typically several decades. This support consists of providing all resources needed for system upkeep, such as service engineers, tools, and spare parts. Spare parts management is usually demanding because of the combination of the large variety of parts, the presence of many expensive slow movers, a geographically dispersed installed base, and the often high costs of system downtime. This leads asset owners to request high service levels from maintenance providers, including the availability of sufficient spare parts. Examples of advanced capital goods can be found in manufacturing equipment for the high-tech industry, healthcare and communication systems, and defence equipment.
In our presentation, we give an overview how Additive Manufacturing (AM) technology may benefit after-sales service supply chains. Furthermore, we outline our past research activities in this field. Particularly, these include the initial identification of promising spare parts for the applications of AM or the question how companies are supposed to incorporate anticipated AM cost reductions in their after-sales service strategy. We conclude our presentation with the hypothesis that the focus of the AM community on design improvements may misinform about the value of AM in after-sales service supply chains.
- Srinivas Vanapalli
The Scope of Additive Manufacturing in Cryogenics, Component Design, and Applications
Additive manufacturing techniques using composites or metals are rapidly gaining momentum in cryogenic applications. Small or large, complex structural components are now no longer limited to mere design studies but can now move into the production stream thanks to new machines on the market that allow for light-weight, cost optimized designs with short turnaround times. The potential for cost reductions from bulk materials machined to tight tolerances has become obvious. Furthermore, additive manufacturing opens doors and design space for cryogenic components that to date did not exist or were not possible in the past, using bulk materials along with elaborate and expensive machining processes, e.g. micromachining. The cryogenic engineer now faces the challenge to design toward those new additive manufacturing capabilities. Additionally, re-thinking designs toward cost optimization and fast implementation also requires detailed knowledge of mechanical and thermal properties at cryogenic temperatures. In the talk a possible roadmap for additive manufacturing applications of parts and components typically used in cryogenic engineering designs will be showcased.
- Stefan Luding
Multiscale Modeling Approaches for Powders in Additive Manufacturing
The dynamic behavior of particulate and granular matter – like sand, powder, suspended particles, often with a wide distribution of particle sizes – is of considerable interest in a wide range of industries and research disciplines since they can behave both solid- or fluid-like. The related mechanisms/processes in particle systems are active at multiple scales (from nanometers at the contact scale to meters in industrial processes) and finding e.g. the reasons for natural disasters like avalanches on even larger scales of kilometres is an essential challenge for both science and application. Modern applications like additive manufacturing (AM) pose various challenge by themselves, but can be approached with the same tools and methods that involve discrete particle models, experiments and theories.
One serious challenge for modeling of AM is the fact that the whole process chain from the initial powder material, to spreading, to laser sintering or melting, cool-down, and the final product testing and application has to be understood and modeled. Examples of multi-scale simulations related to additive manufacturing, are flows of particles/fluids in narrow channels/pores, dosing of cohesive fine powders, avalanche flows on inclined slopes, segregation/mixing behavior, rheology testing in ring-shear cells, all concerning the flow behavior of particles in the AM stages of transport, spreading and preparation. The laser heat input then leads to partial or complete melting of particles which poses many multi-scale and multi-physics problems, until the final product - after cool-down, has to be understood concerning its non-linear elasto-plastic material mechanics related to the performance or failure of solid materials and devices.
- Thomas Weinhart
Particle-Scale and Multi-Scale Modeling of Additive Manufacturing Processes in MercuryDPM
MercuryDPM is an open-source software for particulate and granular matter on the micro-scale: It simulates the motion of individual powder particles according to prescribed contact and external forces. Additional physical effects like wetting, heating, agglomeration, etc have been added to simulate a wide range of industrial and geotechnical processes. Here, we show how MercuryDPM is being used to model powder-based AM processes, such as Powder-Bed Printing. This includes models for particle deposition; sintering and melting of particles; and how to extract macro-scale information from particle-based models. We also show our vision for an integrated software environment for multiscale modeling of AM processes, using MercuryDPM on the micro-scale and the oomph-lib Finite Element solver on the macro-scale.
- Tom Vaneker
Two decades of Rapid Prototyping and Additive Manufacturing within DPM
With the start of Industrial Design at the University of Twente in 2001, product design, and with that the need for rapid prototyping, was also introduced within the department DPM. During these 18 years the role of AM within changed, from usage over industrial advisory into research into fundamental aspects of process, design for AM and AM process development. This presentation will give a short overview of the variance of topics that have been addressed in the last 18 years.
Click here to see details in PDF format.